Fabrication and properties of Fe matrix composites reinforced by macro-particles
-
摘要: 顆粒與基體之間難以均勻穩定的混合以及二者的界面結合強度較差是限制顆粒增強金屬基復合材料制備以及推廣應用的共性關鍵問題,而目前的主要解決措施"預制體法"以及"潤濕化預處理技術"又存在生產效率較低、制備成本較高等問題.基于此,在液態模鍛的基礎上,提出了不做預制體、也不進行潤濕化預處理的制備顆粒增強金屬基復合材料的新技術——"隨流混合+高壓復合"技術,并采用此方法成功制備了復合效果良好的ZTA/KmTBCr26抗磨復合材料.研究了ZTA/KmTBCr26復合材料的微觀組織、硬度以及沖擊性能,發現復合材料內部顆粒分布比較均勻,顆粒與KmTBCr26基體的結合緊密,屬于微機械嚙合.沖擊試驗結果表明,復合材料的沖擊韌性與單一金屬基體相比顯著降低,沖擊斷口形貌顯示材料的斷裂是沿顆粒內部擴展的,沒有出現顆粒的整體脫落,說明陶瓷顆粒與金屬基體具有比較高的結合強度.考察了ZTA/KmTBCr26復合材料與單一KmTBCr26的干摩擦磨損性能,結果表明,低載荷條件下ZTA/KmTBCr26復合材料的磨損性能是KmTBCr26的1.82倍,而高載荷條件下復合材料的磨損性能則是KmTBCr26的3.3倍.Abstract: The basic challenges in the preparation and application of particle-reinforced metal matrix composites are the difficulty in achieving a uniform and stable mixing and the weak bonds between the particles and matrix. At present, these challenges are mainly tackled by making the particles into precursor beforehand and adopting the wetting treatment technologies, respectively. However, these measures can result in lower production efficiency and higher preparation costs. Based on the molten metal die forging process, an innovation technology termed "mixing by the molten metal and cohering by high pressures" was proposed to prepare the metal matrix composites reinforced with ceramic particles without a precursor or wetting them beforehand. Using this technique, a kind of ZTA particles-reinforced KmTBCr26 cast iron wear resistant composite with a good compound effect had been prepared, and the microstructure, hardness, and impact property of the ZTA/KmTBCr26 composite was studied. The study reveals that the particle distribution in the ZTA/KmTBCr26 composite is generally uniform, and the interfacial bonding between ceramic particle and KmTBCr26 matrix is of micromechanical interlocking. The results of impact tests show that the impact toughness of the composites is significantly lower than that of the single metal, and the fracture morphology indicates that the fracture of the composites extends through the ceramic particle instead of the matrix. No particle detachment is observed, which indicates a high bonding strength between the particles and matrix. Furthermore, the dry friction and wear properties of the ZTA/KmTBCr26 composite and KmTBCr26 cast iron were investigated. The results show that the wear resistance of the composite is 1.82 times that of the KmTBCr26 cast iron when the load is lower, while the wear resistance of the composite increased by 3.3 times under the higher load.
-
Key words:
- composite /
- wear white cast iron /
- molten metal die forge /
- impact toughness /
- wear resistance
-
參考文獻
[1] Wiengmoon A, Chairuangsri T, Brown A, et al. Microstructural and crystallographical study of carbides in 30wt.%Cr cast irons. Acta Mater, 2005, 53(15):4143 [2] Miracle D B. Metal matrix composites——from science to technological significance. Compos Sci Technol, 2005, 65(15-16):2526 [3] Akhtar F. Microstructure evolution and wear properties of in situ synthesized TiB2 and TiC reinforced steel matrix composites. J Alloys Compd, 2008, 459(1-2):491 [6] Francois H. Composite Wear Component: USA Patent, 6399176B1. 2002-06-04 [8] Kish O, Froumin N, Aizenshtein M, et al. Interfacial interaction and wetting in the Ta2O5/Cu-Al system. J Mater Eng Perform, 2014, 23(5):1551 [10] Liu A G, Guo M H, Zhao M H, et al. Microstructure and wear resistance of large WC particles reinforced surface metal matrix composites produced by plasma melt injection. Surf Coat Technol, 2007, 201(18):7978 [12] Edelbauer J, Schuller D, Lott O, et al. High temperature squeeze casting of nickel based metal matrix composites with interpenetrating microstructure. Mater Sci Forum, 2015, 825-826:93 [15] Malomo B O, Fadodun O O, Oluwasegun K M, et al. The effect of controlled melt-solidification on the strain rate sensitivity of a squeeze-cast hybrid-reinforced aluminum AA 6061 matrix composite. Int J Eng Res Afr, 2015, 16:1 [16] Gurusamy P, Balasivanandha P S. Effect of the squeeze pressure on the mechanical properties of the squeeze cast Al/SiCp metal matrix composite. Int J Microstruct Mater Prop, 2013, 8(4-5):299 [17] Llorca J, Martin A, Ruiz J, et al. Particulate fracture during deformation of a spray formed metal-matrix composite. Metall Trans A, 1993, 24(7):1575 [18] Turnbull A, De Los Rios E R. The effect of grain size on fatigue crack growth in an aluminum magnesium alloy. Fatigue Fract Eng Mater Struct, 1995, 18(11):1355 [20] Kamat S V, Hirth J P, Mehrabian R. Mechanical properties of particulate-reinforced aluminum-matrix composites. Acta Mater, 1989, 37(9):2395 [22] Ashby M F, Abulawi J, Kong H S. Temperature maps for frictional heating in dry sliding. Tribol Trans, 1991, 34(4):577 -
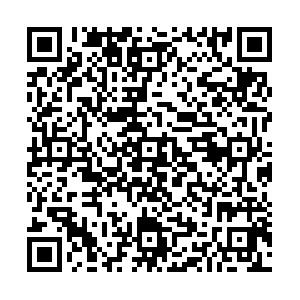
計量
- 文章訪問數: 760
- HTML全文瀏覽量: 233
- PDF下載量: 17
- 被引次數: 0