Effects of an orthogonal magnetic field on discharge craters created during the single-spark electrical discharge machining process
-
摘要: 電火花放電通道在正交磁場的作用下向洛倫茲力方向偏轉、延伸,進而導致電蝕凹坑形貌發生變化,研究磁場輔助電火花加工(MF-EDM)過程中電蝕凹坑的形貌變化規律及特點,對進一步明晰電火花加工機理具有重要意義. 基于MF-EDM氣中單脈沖放電試驗,使用表面輪廓儀觀測電蝕凹坑延伸長度、深度、寬度及放電起始點偏移量,并得出磁場及放電參數對電蝕凹坑的影響規律. 結果表明:電蝕凹坑長度隨著磁感應強度、開路電壓的增大而增大;電極外伸長度的影響結果相反;電蝕凹坑深度隨著磁感應強度、開路電壓、電極外伸長度的增加沒有明顯的變化規律;電容與磁感應強度存在最優參數組合以使凹坑長度最大;隨著磁感應強度及放電能量的增加放電起始點的偏移量增加.Abstract: In the single-spark electrical discharge machining (EDM) process under the action of an orthogonal magnetic field, the plasma from the electric discharge is deflected and extends to the direction of the Lorenz force, which leads to a change in the discharge craters compared with traditional EDM. In this paper, the morphology and characteristics of craters created during the process of magnetic field assisted electrical discharge machining (MF-EDM) were studied. The results of this study may be applied to production practice, and it is expected that the machining of tapered holes can be realized using magnetic field assisted EDM. Based on single-pulse MF-EDM in gas, the crater morphology was observed using a surface topography instrument. During the experiment the voltage waveform was obtained using an oscilloscope and the current waveform was calculated using the simulation software SABER. After measuring the distribution of the orthogonal magnetic field, the ampere force of the electrode at the moment of discharge was calculated. The deformation of the end of the electrode was obtained using simulation software ANSYS15.0. The offset of the starting point of the discharge under the influence of the orthogonal magnetic field was proven. Then, rules for the effects of the magnetic field and discharge parameters on the craters were obtained. The results indicate that crater length increases with an increase in magnetic field intensity and open circuit voltage, but the influence of the electrode overhang length shows the opposite. There is no obvious change rule for crater depth with an increase in magnetic field intensity, open circuit voltage, or electrode overhang length. To obtain the maximum length or minimum depth of the crater, an optimum combination of the capacitance and magnetic field intensity can be used. With an increase in magnetic induction intensity and discharge energy, the offset of the discharge point increases.
-
參考文獻
[1] Manesh K K, Narayanan A A. Numerical simulation ofmagnetic field-assisted material removal in micro-EDM. Mater Sci Forum, 2015, 830-831:104 [5] Heinz K, Kapoor S G, DeVor R E, et al. An investigation of magnetic-field-assisted material removal in micro-EDM for nonmagnetic materials. J Manuf Sci Eng, 2011, 133(2):021002 [6] Teimouri R, Baseri H. Effects of magnetic field and rotary tool on EDM performance. J Manuf Processes, 2012, 14(3):316 [7] Yeo S H, Murali M, Cheah H T. Magnetic field assisted micro electro-discharge machining. J Micromech Microeng, 2004, 14(11):1526 [8] Govindan P, Gupta A, Joshi S S, et al. Single-spark analysis of removal phenomenon in magnetic field assisted dry EDM. J Mater Process Technol, 2013, 213(7):1048 [9] Joshi S, Govindan P, Malshe A, et al. Experimental characterization of dry EDM performed in a pulsating magnetic field. CIRP Ann, 2011, 60(1):239 [12] Shang J S, Surzhikov S T, Kimmel R, et al. Mechanisms of plasma actuators for hypersonic flow control. Prog Aerospace Sci, 2005, 41(8):642 [13] Zaidi S H, Smith T, Macheret S, et al. Snowplow surface discharge in magnetic field for high speed boundary layer control//44th AIAA Aerospace Sciences Meeting and Exhibit. Reno, 2006:1006-1 [14] Leonov S, Bityurin V, Yarantsev D, et al. High-speed flow control due to interaction with electrical discharges//AIAA/CIRA 13th International Space Planes and Hypersonics Systems Technologies Conference. Capua, 2005:3287-1 -
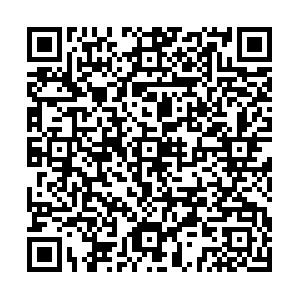
計量
- 文章訪問數: 752
- HTML全文瀏覽量: 251
- PDF下載量: 15
- 被引次數: 0