Friction properties of C-containing ceramic coatings on an Mg-Li alloy
-
摘要: 通過在Na2SiO3-KOH基礎電解液中加入石墨烯添加劑,在鎂鋰合金表面制備出一層自潤滑的含碳陶瓷層. 利用掃描電鏡、原子力顯微鏡以及X射線衍射儀分析了陶瓷層的表面形貌、粗糙度以及物相組成,利用摩擦磨損試驗儀對陶瓷層在室溫下的摩擦學性能進行研究. 其結果表明,加入石墨烯后制備出的含碳陶瓷層表面放電微孔分布均勻,且其微孔尺寸和表面粗糙度均明顯降低. 相比于鎂鋰合金,陶瓷層的表面硬度也得到明顯的提高. 此外,含碳陶瓷層主要由SiO2、Mg2SiO4以及MgO物相組成,而石墨烯則以機械形式彌散分布于陶瓷層中并起到減摩作用. 當石墨烯體積分數為1%時,陶瓷層表面顯微硬度為1317.6 HV0.1 kg,其摩擦系數僅為0.09,其耐磨性明顯提高. 同時,陶瓷層磨痕的深度和寬度均明顯小于鎂鋰合金,而且較為光滑,表明陶瓷層表面沒有發生嚴重的黏著磨損.Abstract: Due to its specific strength, superior electromagnetic shielding and excellent processing capabilities, the magnesium-lithium (Mg-Li) alloy is regarded as one of the most promising structural metal materials and has been extensively applied in various fields such as aerospace, offshore engineering, and the communication industry. Unfortunately, inferior tribological behavior, caused by low hardness, a fluctuating friction coefficient, and serious adhesive wear, has severely inhibited large-scale application of Mg-Li alloys in industrial engineering. Therefore, in this study, to enhance the tribological performance of a micro-arc oxidation (MAO)-produced ceramic coating on an Mg-Li alloy, a variety of inorganic particles were tentatively added to MAO electrolytes to prepare composite ceramic coatings with pronounced friction and wear resistance properties. MAO in Na2SiO3-KOH electrolytes with graphene additives was used to produce self-lubricating C-containing ceramic coatings on an Mg-Li alloy. The surface morphologies, roughness, hardness, and phase compositions were investigated using scanning electron microscopy (SEM), atomic force microscopy (AFM), a Vickers hardness test, and X-ray power diffraction (XRD). At room temperature, the tribological properties of the ceramic coatings were evaluated by friction and wear tests. The results indicate that the micro-pores in the C-containing coatings distribute uniformly on the alloy surfaces and a significant decrease in micro-pore size and surface roughness is observed. The surface hardness of the coatings show significant enhancement compared with that of the Mg-Li alloy. The coatings mainly consist of SiO2, Mg2SiO4, and MgO phases; graphene is dispersed throughout via mechanical effects and displayed an antifriction effect. The C-containing coating produced when the volume fraction of graphene in the electrolyte is 1% show good wear resistance and its surface hardness and friction coefficient are 1317.6 HV0.1 kg and 0.09, respectively. Meanwhile, compared with the Mg-Li alloy the wear traces on the coating appears narrower and shallow, and the worn area seems relatively smooth, which indicates that slight adhesive wear occurs on the C-containing coating surface.
-
Key words:
- magnesium-lithium alloy /
- graphene /
- micro-arc oxidation /
- antifriction property /
- wear resistance
-
參考文獻
[2] Laleh M, Rouhaghdam A S, Shahrabi T, et al.Effect of alumina sol addition to micro-arc oxidation electrolyte on the properties of MAO coatings formed on magnesium alloy AZ91D. J Alloys Compd, 2010, 496(1-2):548 [4] Matykina E, Arrabal R, Monfort F, et al. Incorporation of zirconia into coatings formed by DC plasma electrolytic oxidation of aluminium in nanoparticle suspensions.Appl Surf Sci, 2008, 255(5):2830 [5] Chen F, Zhou H, Yao B, et al. Corrosion resistance property of the ceramic coating obtained through microarc oxidation on the AZ31 magnesium alloy surfaces. Surf Coat Technol, 2007, 201(9-11):4905 [6] Yang Y, Liu Y H. Effects of current density on the microstructure and the corrosion resistance of alumina coatings embedded with SiC nano-particles produced by micro-arc oxidation. J Mater Sci Technol, 2010, 26(11):1016 [7] Li X J, Luan B L. Discovery of Al2O3 particles incorporation mechanism in plasma electrolytic oxidation of AM60B magnesium alloy. Mater Lett, 2012, 86:88 [8] Lü G H, Chen H, Gu W C, et al.Effects of graphite additives in electrolytes on the microstructure and corrosion resistance of alumina PEO coatings. Curr Appl Phys, 2009, 9(2):324 [9] Snizhko L O, Yerokhin A L, Pilkington A, et al. Anodic processes in plasma electrolytic oxidation of aluminium in alkaline solutions.Electrochim Acta, 2004, 49(13):2085 [10] Dunleavy C S, Golosnoy I O, Curran J A, et al. Characterisation of discharge events during plasma electrolytic oxidation. Surf Coat Technol, 2009, 203(22):3410 [11] Feng C J, Hu S L, Jiang Y F, et al. Effects of micro-arc oxidation of Ti6Al4V alloy on adhesion property to electroless Ni-P-ZrO2 composite platings and their wear resistance. Rare Met Mater Eng, 2013, 42(12):2427 [12] Abbasi S, Golestani-Fard F, Rezaie H R, et al.MAO-derived hydroxyapatite/TiO2 nanostructured multi-layer coatings on titanium substrate. Appl Surf Sci, 2012, 261:37 [13] Ma K J, Bosta M M S A, Wu W T. Preparation of self-lubricating composite coatings through a micro-arc plasma oxidation with graphite in electrolyte solution. Surf Coat Technol, 2014, 259:318 [14] Mohammadi S, Taromi F A, Shariatpanahi H, et al. Electrochemical and anticorrosion behavior of functionalized graphite nanoplatelets epoxy coating.J Ind Eng Chem, 2014, 20(6):4124 [15] Hua Y, Zhang Z G, Li W. Microstructure and degradation properties of C-containing composite coatings on magnesium alloy wires treated with micro-arc oxidation. Surf Coat Technol, 2016, 291:70 [16] Wu X H, Su P B, Jiang Z H, et al. Influences of current density on tribological characteristics of ceramic coatings on ZK60 Mg alloy by plasma electrolytic oxidation. ACS Appl Mater Interfaces, 2010, 2(3):808 [17] Tsao L C. Interfacial structure and fracture behavior of 6061 Al and MAO-6061 Al direct active soldered with Sn-Ag-Ti active solder. Mater Des, 2014, 56:318 [18] Li H X, Song R G, Ji Z G. Effects of nano-additive TiO2 on performance of micro-arc oxidation coatings formed on 6063 aluminum alloy. Trans Nonferrous Met Soc China, 2013, 23(2):406 -
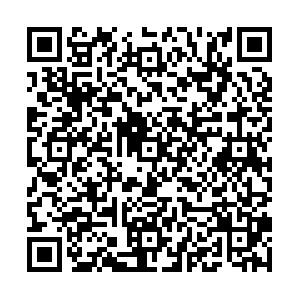
計量
- 文章訪問數: 741
- HTML全文瀏覽量: 288
- PDF下載量: 13
- 被引次數: 0