Research and development of a heat-source model in numerical simulations for the arc welding process
-
摘要: 焊接過程的數值模擬作為一種有效的計算手段,在焊接溫度場及殘余應力分布的評價中獲得了廣泛應用,而焊接熱源模型的選擇及模型參數的確定直接影響到計算和評價結果的準確性.本文通過對近年來常用的電弧焊接熱源模型進行梳理,介紹了其研究進展,分析了不同熱源模型的特點及適用性.高斯面熱源模型和雙橢球體熱源模型作為基礎熱源模型,廣泛應用于較小尺寸工件和規則軌跡的焊接過程數值模擬,且具有較高的計算精度;簡化熱源模型和溫度替代型熱源模型多用于大厚工件的多層多道焊接及復雜軌跡焊接過程的數值模擬,能夠實現效率和精度的統一;多絲電弧焊接熱源較為復雜,采用修正后的雙橢球體疊加熱源模型,計算結果能保證一定的精度;結合型熱源模型對熔池形狀的描述更靈活,在深熔電弧焊的數值模擬中具有優勢.本文可為電弧焊接過程數值模擬的熱源模型選擇和模型參數確定提供有益參考.Abstract: As an effective computational method, the numerical simulation of welding processes has been widely used in evaluating welding temperature fields and residual stress distributions. In the numerical simulation process, the selection of the welding heatsource model and the confirmation of model parameters will directly affect the accuracy of the calculation and the evaluation results. Some heat-source models commonly used in numerical simulations of the arc welding process were surveyed in this article; advances in their development were introduced, and their characteristics and applicability were analyzed. As basic heat-source models, the Gauss surface heat-source modes and double-ellipsoid-volume heat-source model have been widely used in the numerical simulation of arc welding for workpieces with a relatively small size and a regular welding trajectory, and the calculation results have been demonstrated to be accurate. In the numerical simulation of arc welding processes for large and thick workpieces welded using multi-layer or multipass techniques and for workpieces with a complex welding trajectory, the simplified heat-source model and temperature-substitution heat-source model are chiefly applied, and the calculation efficiency and precision can be well balanced. The heat source of multi-wire arc welding is comparatively complicated, and the superposed model of modified double-ellipsoid-volume heat-source models can ensure a certain accuracy of the calculation results. The combined heat-source model is more flexible in the shape description of the molten pool and has advantages in the numerical simulation of arc welding with deep penetration. The all-around induction and analyses in this article are expected to provide valuable reference and guidance for the selection of a heat-source model and for confirming model parameters in the numerical simulation of arc welding processes.
-
參考文獻
[2] Huang X F, Liu Z W, Xie H M. Recent progress in residual stress measurement techniques. Acta Mech Solida Sin, 2013, 26(6):570 [7] Pavelic V, Tanbakuchi R, Uyehara O A, et al. Experimental and computed temperature histories in gas tungsten-arc welding of thin plates. Weld J, 1969, 48(7):295 [10] Goldak J, Chakravarti A, Bibby M. A new finite element model for welding heat sources. Metall Trans B, 1984, 15(2):299 [15] Azar A S, Ås S K, Akselsen O M. Determination of welding heat source parameters from actual bead shape. Comput Mater Sci, 2012, 54:176 [17] Tekriwal P, Mazumder J. Finite element analysis of three-dimensional transient heat transfer in GMA welding. Weld J, 1988, 67(7):150s [20] Bae D H, Kim C H, Cho S Y, et al. Numerical analysis of welding residual stress using heat source models for the multi-pass weldment. KSME Int J, 2002, 16(9):1054 [21] Kiyoshima S, Deng D A, Ogawa K, et al. Influences of heat source model on welding residual stress and distortion in a multipass J-groove joint. Comput Mater Sci, 2009, 46(4):987 [22] Deng D A, Kiyoshima S, Ogawa K, et al. Predicting welding residual stresses in a dissimilar metal girth welded pipe using 3D finite element model with a simplified heat source. Nucl Eng Des, 2011, 241(1):46 [27] Cho D W, Kiran D V, Song W H, et al. Molten pool behavior in the tandem submerged arc welding process. J Mater Process Technol, 2014, 214(11):2233 [35] Keppas L K, Wimpory R C, Katsareas D E, et al. Combination of simulation and experiment in designing repair weld strategies:a feasibility study. Nucl Eng Des, 2010, 240(10):2897 [36] Ohms C, Wimpory R C, Katsareas D E, et al. NET TG1:residual stress assessment by neutron diffraction and finite element modeling on a single bead weld on a steel plate. Int J Press Ves Pip, 2009, 86(1):63 [38] Bachorski A, Painter M J, Smailes A J, et al. Finite-element prediction of distortion during gas metal arc welding using the shrinkage volume approach. J Mater Process Technol, 1999, 9293:405 [39] Zheng Z T, Shan P, Hu S S, et al. Numerical simulation of gas metal arc welding temperature field. China Weld, 2006, 15(4):55 -
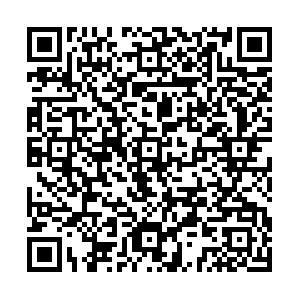
計量
- 文章訪問數: 1068
- HTML全文瀏覽量: 377
- PDF下載量: 84
- 被引次數: 0