Physical simulation of the position and evolution process of dust accumulation in the bustle pipe of a COREX shaft furnace
-
摘要: 建立COREX豎爐三維半周物理模型,模擬豎爐圍管粉塵初始堵塞位置及其演變過程,考察鼓風量、排料速度、非工況排料等操作條件對圍管粉塵堵塞的影響.模擬結果顯示,COREX豎爐圍管初始堵塞位置為AGD架梁圓管前方的8#~12#導氣槽區域.當導氣槽前端填充床內形成粉塵沉積區后,若沉積區向上發展速度大于其隨物料向下運動速度,粉塵沉積區向圍管方向發展,并逐步堵塞圍管導氣槽,進而在圍管內形成粉塵堆積區.該堆積區在圍管內繼續發展,使得其堆腳向圍管遠端運動,從而逐步將遠端導氣槽堵塞.此外,模擬發現隨著排料速度加快及鼓風量增加,圍管內不易發生粉塵堵塞.當爐內非工況條件發生時,粉塵堆積的動態平衡被打破,易造成圍管內粉塵的堆積堵塞.Abstract: A 3D semi-cylindrical physical model of COREX shaft furnace was established, and the initial position and evolution process of dust accumulation in the bustle pipe of a shaft furnace were investigated through this model. The effects of discharging rate, gas flow rate, and non-normal operation condition on dust accumulation in the bustle pipe were also studied. The results show that the initial position of dust accumulation in the bustle pipe is in the 8#-12# slot region, located before the supporting tube of AGD beam. The dust blockage is first formed in the packed bed near the slot and then blocks the slot and grows into the bustle pipe if the growth velocity of the blockage region is greater than the descending velocity. Finally, dust accumulation can be observed in the bustle pipe. The dust accumulation is still growing in the bustle pipe, and the edge of the dust pile could develop to the far side; thus, the other slots would be gradually clogged by dust. Moreover, the results confirm that with increased discharge and gas flow rates, dust accumulation in the bustle pipe is greatly hindered. In contrast, under non-normal operation conditions, the dynamic balance of dust blockage is broken, and dust accumulation in bustle pipe is easily formed.
-
Key words:
- COREX shaft furnace /
- bustle pipe /
- dust accumulation /
- physical simulation /
- areal gas distribution
-
參考文獻
[1] Kurunov I F. The direct production of iron and alternatives to the blast furnace in iron metallurgy for the 21st century. Metallurgist, 2010, 54(5-6):335 [2] Qu Y X, Yang Y X, Zou Z S, et al. Thermal decomposition behaviour of fine iron ore particles. ISIJ Int, 2014, 54(10):2196 [8] Zhou H, Luo Z G, Zhang T, et al. 3D numerical simulation of the influence of AGD beams on gas distribution in COREX-3000 shaft furnace. Adv Mater Res, 2013, 712-715:1268 [9] Wu S L, Du K P, Xu J, et al. Numerical analysis on effect of areal gas distribution pipe on characteristics inside COREX shaft furnace. JOM, 2014, 66(7):1265 [10] Zhou H, Luo Z G, Zou Z S, et al. Experimental study on burden descending behavior in COREX shaft furnace with AGD beams. Steel Res Int, 2015, 86(9):1073 [11] Zhou H, Luo Z G, Zhang T, et al. Analyses of solid flow in COREX shaft furnace with AGD by discrete element method. Ironmaking Steelmaking, 2015, 42(10):774 [12] Zhou H, Luo Z G, Zhang T, et al. DEM study of solid flow in COREX shaft furnace with areal gas distribution beams. ISIJ Int, 2016, 56(2):245 [13] Ichida M, Nishihara K, Tamura K, et al. Influence of ore/coke distribution on descending and melting behavior of burden in blast furnace. ISIJ Int, 1991, 31(5):505 [14] Takahashi H, Tanno M, Katayama J. Burden descending behaviour with renewal of deadman in a two dimensional cold model of blast furnace. ISIJ Int, 1996, 36(11):1354 [15] Wright B, Zulli P, Zhou Z Y, et al. Gas-solid flow in an ironmaking blast furnace-I:physical modelling. Powder Technol, 2011, 208(1):86 -
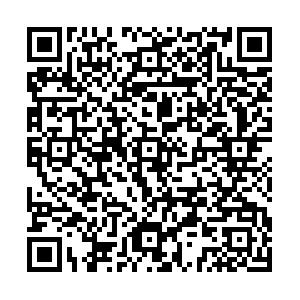
計量
- 文章訪問數: 960
- HTML全文瀏覽量: 272
- PDF下載量: 14
- 被引次數: 0