Morphology prediction of cold-sprayed Cu and Al coatings through multi-particles deposition simulation
-
摘要: 采用有限元軟件ANSYS/LS-DYNA建立了15個顆粒與基板的冷噴涂沉積模型,通過多顆粒沉積模型預測工藝條件、不同顆粒/基板組合的沉積行為和微觀形貌;制備了Al和Cu冷噴涂涂層,觀察了涂層截面形貌和顆粒變形特征,并與模擬結果進行對比.結果表明,多顆粒沉積模型可預測噴涂條件對顆粒沉積過程及涂層微觀特征的影響,以及不同顆粒/基板組合的界面微觀形貌.當碰撞速度低時,顆粒變形不充分,顆粒交界處易形成孔洞;隨著速度增加,顆粒流變填充孔洞,涂層致密.與顆粒相比,硬基板涂層/基板界面平滑,機械互鎖作用小;軟基板形成射流狀金屬擠入顆粒之間,增加結合作用.Abstract: A deposition model of 15 particles onto a substrate was established using the finite element program ANSYS/LS-DYNA. Based on the multi-particle deposition model, the deposition behavior and morphology as well as the interface characteristic were predicted for different particles/substrate cases. Al and Cu coatings were prepared by cold spraying. The cross section of the coatings and the characters of particle deformation were observed by scanning electron microscopy and compared with the simulated results by the multiparticle deposition model. The results demonstrate that the multi-particle deposition model can predict the effect of process conditions on the deposition behavior, microscopic characteristic, and interface morphology for different particles/substrate cases. When the impact velocity is low, particle deformation is not sufficient, which easily results in holes at the junction of particles; however, the holes disappear gradually with increasing impact velocity. Compared with particles, for a hard substrate, the coatings/substrate interface is smooth, which weakens the interlock; while for a soft substrate, the substrate deforms severely to form jet-like metal, which squeezes into particles to increase the bonding.
-
Key words:
- spraying /
- coatings /
- morphology /
- computer simulation /
- finite element method /
- deposition /
- interfaces
-
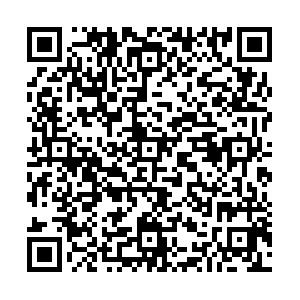
計量
- 文章訪問數: 278
- HTML全文瀏覽量: 80
- PDF下載量: 6
- 被引次數: 0