Selective extraction of heavy metals Cr,Ni and Zn from stainless steel-making dust
-
摘要: 基于熱力學計算結果,通過配碳還原-熔分工藝,從不銹鋼粉塵中選擇性分步提取了Cr、Ni和Zn重金屬元素.配碳還原實驗結果表明,不銹鋼粉塵的最佳配碳量為20%,粉塵中Fe、Ni和Zn的最低還原溫度為1050℃,Cr的最低還原溫度是1 400℃,與熱力學計算結果一致,通過控制溫度實現了對粉塵中金屬的選擇性分步還原.直接還原熔分實驗說明,Fe-Cr合金最佳熔分溫度為1550℃,粉塵中金屬以Fe-Ni-Cr合金形式被提取出來,渣金分離狀況良好,反應時間5min時金屬提取率已達到75%左右,15 min時Fe和Cr收得率達到85%以上,Ni超過90%.通過控制配碳量、還原時間與反應溫度,在不改變現有工藝的條件下,不銹鋼粉塵直接返回煉鋼主流程回收其重金屬完全可行.Abstract: Heavy metal elements such as Cr, Ni and Zn were extracted from stainless steel-making dust through the direct reduction and melting process on the basis of thermodynamic analysis. Carbon deoxidization experiment results show that the optimal carbon addition percentage in the dust is 20%, and the lowest reduction temperature is 1 050℃ for Fe, Ni and Zn and 1 400℃ for Cr, which are in agreement with the thermodynamic calculation results. These metals can be selectively reduced through controlling the temperature. According to direct reduction and melting experiment results, the optimal melting temperature of the Fe-Cr alloy is 1 550℃, metals in the dust are extracted as the Fe-Ni-Cr alloy, and the slag is separated from the metals quite well. The metal extraction rate is about 75% after 5 min reaction; but after 15 min reaction the Fe and Cr extraction rates surpass 85%, while the Ni extraction rate is over 90%. These experimental results indicate that it is completely feasible to return the stainless steel-making dust to the steel-making main flow and recycle its heavy metals by controlling the carbon content, reduction time and temperature without modifying the present process.
-
Key words:
- stainless steel /
- dust /
- heavy metals /
- selective extraction /
- direct reduction process /
- melting /
- waste utilization
-
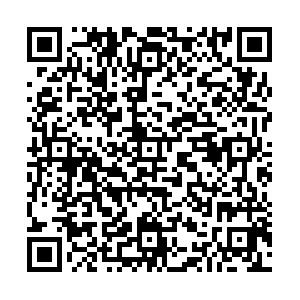
計量
- 文章訪問數: 191
- HTML全文瀏覽量: 41
- PDF下載量: 11
- 被引次數: 0