Electromechanical vibration control of the main drive of a rolling mill based on auto-disturbance-rejection control technology
-
摘要: 軋機驅動電機與軋輥間采用長軸連接,連接軸剛度有限,因此在帶材高速軋制時,常規電流、轉速雙閉環控制易產生機電振動和斷帶現象.為了克服該缺陷,針對軋機主傳動系統精確模型不易獲得的特點,將不確定外擾和未建模動態視為一個綜合擾動項,運用擴張狀態觀測器對系統狀態和綜合擾動項進行觀測,設計了軋機主傳動機電振動擴張狀態觀測器控制系統;進一步利用自抗擾控制技術設計了一個不依賴于對象模型的軋機主傳動機電振動控制系統.仿真研究結果表明兩種控制系統都有效改善了軋機主傳動系統的跟蹤性能,抑制了系統的機電振動現象,同時對系統內部參數如軋輥轉動慣量等的攝動也具有較強的魯棒性.首次將擴張狀態觀測器和自抗擾控制技術應用到軋機主傳動機電振動控制系統中,并通過與傳統電流、轉速雙PI控制和基于降維狀態觀測器的狀態反饋控制比較,證明了該方法的有效性和優越性.Abstract: For the distance between the drive motor and roll of a rolling mill is long and the rigid of its spindle is limited, the normal control of current and speed closed loops leads easily to the phenomena of electromechanical vibration and broken strip as the strip is rolled at high speed. In order to solve the problem, aiming at the characteristics of the approximate model of a main drive system, the uncertain external load disturbance and unmodeled dynamics were regarded as one integrated disturbance. Electromechanical vibration controllers were designed based on extended state observer (ESO) and auto-disturbance-rejection control (ADRC) technology respectively. Simulated results show that the two controllers effectively improve the performances of command following, electromechanical vibration suppression, and robustness to parameter variation. ESO and ADRC were utilized in electromechanical vibration control of the main drive system of a rolling mill, their validity and superiority were verified in comparison with the conventional PI controller and the state feedback controller based on reduced-order state observer.
-
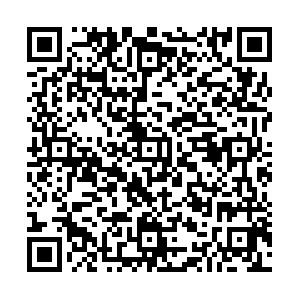
計量
- 文章訪問數: 159
- HTML全文瀏覽量: 22
- PDF下載量: 8
- 被引次數: 0